نحوه تنظیم پارامترهای بهینه برای اینورتر صنعتی در صنایع مختلف
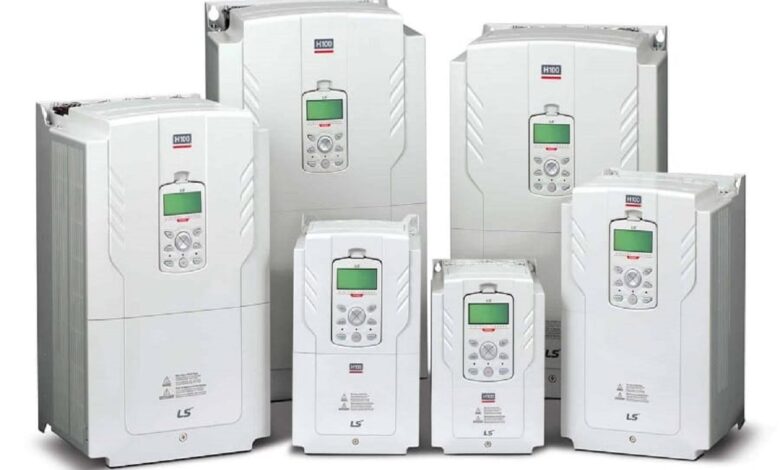
اینورتر صنعتی یا درایو فرکانس متغیر (VFD)، به عنوان یکی از اجزای حیاتی در سیستمهای کنترلی و اتوماسیون صنعتی، به مهندسان امکان کنترل دقیق سرعت و گشتاور موتورهای الکتریکی را میدهد.
اینورتر صنعتی یا درایو فرکانس متغیر (VFD)، به عنوان یکی از اجزای حیاتی در سیستمهای کنترلی و اتوماسیون صنعتی، به مهندسان امکان کنترل دقیق سرعت و گشتاور موتورهای الکتریکی را میدهد. تنظیم پارامترهای بهینه در این دستگاهها نقش مهمی در بهبود کارایی، کاهش هزینههای انرژی، افزایش عمر موتور و تجهیزات و کاهش خطاهای احتمالی دارد. با توجه به رشد روزافزون استفاده از اینورترها در صنایع مختلف، دانش تخصصی در زمینه تنظیمات بهینه، امری ضروری محسوب میشود.
در این مقاله سعی شده است تا با استفاده از هدینگهای متنوع و بخشبندیهای تخصصی، مباحث مرتبط با بهینهسازی پارامترهای اینورتر صنعتی به تفصیل بیان گردد. همچنین نکات مهم و چالشهای مرتبط با تنظیم این دستگاهها در محیطهای صنعتی مختلف نیز مورد بررسی قرار میگیرد.
درایو اینورتر چیست و چه کاربردی دارد؟
برای آشنایی بیشتر با اصول عملکرد این تجهیزات، بهتر است ابتدا بدانیم درایو اینورتر صنعتی چیست و چه نقشی در بهینهسازی سیستمهای الکتریکی دارد. اینورتر صنعتی دستگاهی است که انرژی ورودی الکتریکی با ولتاژ و فرکانس ثابت را به انرژی خروجی با ولتاژ و فرکانس متغیر تبدیل میکند. این ویژگی به مهندسان این امکان را میدهد که بتوانند سرعت و گشتاور موتورهای الکتریکی را به دقت کنترل کنند. از کاربردهای رایج اینورتر در صنایع مختلف میتوان به موارد زیر اشاره کرد:
- کنترل سرعت موتورهای پمپ، کمپرسور و فن: کاهش مصرف انرژی و افزایش بهرهوری سیستمهای حرارتی و تهویه.
- کاهش سایش و فرسودگی: با کنترل دقیق شروع و توقف موتور، خطر خرابیهای مکانیکی کاهش مییابد.
- بهینهسازی مصرف انرژی: تنظیم دقیق پارامترهای کارکرد موتورها موجب کاهش مصرف انرژی و بهبود عملکرد سیستمهای صنعتی میشود.
اصول عملکرد اینورترهای صنعتی
عملکرد اینورترهای صنعتی بر مبنای تبدیل جریان مستقیم (DC) به جریان متناوب (AC) استوار است. در فرآیند تبدیل، چندین مرحله کلیدی وجود دارد:
- تبدیل AC به DC: ابتدا برق ورودی با فرکانس ثابت به DC تبدیل میشود.
- فیلترسازی و تثبیت: در این مرحله، نوسانات احتمالی و هارمونیکها حذف میشوند.
- تبدیل DC به AC با فرکانس متغیر: در نهایت، انرژی DC به AC با فرکانس و ولتاژ مورد نیاز تبدیل میشود.
این فرآیند به مهندسان اجازه میدهد تا بتوانند تنظیمات متنوعی بر روی پارامترهای خروجی اعمال کنند تا بهترین عملکرد سیستم تضمین شود.
اهمیت تنظیمات بهینه در اینورترهای صنعتی
تنظیمات بهینه در اینورترهای صنعتی نقش حیاتی در بهبود کارایی، کاهش مصرف انرژی و افزایش طول عمر تجهیزات دارد. با تنظیم صحیح پارامترهایی مانند فرکانس، ولتاژ و منحنیهای شتاب و ترمز، میتوان عملکرد موتورهای الکتریکی را بهینه کرده و از نوسانات ناخواسته جریان جلوگیری کرد.
این امر نه تنها باعث کاهش هزینههای نگهداری و تعمیرات میشود، بلکه بهرهوری سیستم را افزایش داده و از خرابیهای ناگهانی جلوگیری میکند. در بخش زیر به طور تخصصی به دلایل اهمیت تنظیمات بهینه در اینورتر میپردازیم.
بهبود بهره وری انرژی
یکی از مهمترین اهداف تنظیمات بهینه، کاهش مصرف انرژی است. با بهینهسازی پارامترهای اینورتر میتوان:
- کاهش هدررفت انرژی: تنظیم دقیق پارامترهای خروجی باعث میشود تا هدررفت انرژی به حداقل برسد.
- افزایش راندمان موتور: کنترل دقیق سرعت و گشتاور موتور باعث میشود که موتور با کارایی بیشتری عمل کند.
- کاهش هزینههای عملیاتی: از آنجایی که مصرف انرژی بهطور مستقیم بر هزینههای عملیاتی تأثیر میگذارد، بهینهسازی این بخش میتواند منجر به کاهش قابل توجه هزینهها شود.
افزایش طول عمر تجهیزات
تنظیمات بهینه میتوانند باعث کاهش سایش و فرسودگی قطعات سیستم شوند. این موضوع به دلایل زیر اهمیت دارد:
- کاهش حرارت و ارتعاشات: کنترل دقیق پارامترهای جریان و ولتاژ باعث کاهش تولید حرارت و ارتعاشات میشود.
- پیشگیری از خطاهای ناشی از نوسانات: پارامترهای بهینه میتوانند از ایجاد نوسانات شدید جلوگیری کرده و عمر مفید موتور و تجهیزات را افزایش دهند.
- افزایش قابلیت اطمینان سیستم: سیستمهای بهینه شده در مقابل خطاها و اختلالات محیطی مقاومتر عمل میکنند.
بهبود کیفیت فرآیندهای صنعتی
در صنایع تولیدی و فرآیندی، کیفیت خروجی محصولات نقش مهمی دارد. تنظیمات دقیق و بهینه اینورترها به موارد زیر کمک میکند:
- کنترل دقیق سرعت تولید: تنظیمات بهینه اجازه میدهد که سرعت و زمانبندی تولید به صورت دقیق کنترل شود.
- کاهش نوسانات فرآیند: با بهینهسازی پارامترها، نوسانات احتمالی در فرآیند تولید کاهش یافته و کیفیت محصول نهایی بهبود مییابد.
- افزایش دقت در کنترل فرآیند: سیستمهای بهینه، کنترل دقیقتری بر روی عملیات صنعتی دارند که منجر به کاهش خطاها و افزایش بهرهوری میشود.
پارامترهای کلیدی تنظیم اینورتر صنعتی
برای بهینهسازی عملکرد اینورتر صنعتی، چندین پارامتر کلیدی وجود دارد که باید به دقت تنظیم شوند. در ادامه به ۴ تا از مهمترین این پارامترها پرداخته میشود.
ولتاژ خروجی
ولتاژ خروجی یکی از پارامترهای حیاتی در عملکرد موتور و سیستمهای صنعتی محسوب میشود. تنظیم دقیق این ولتاژ تضمین میکند که موتور با گشتاور و سرعت مطلوب عمل کند و از بروز مشکلات ناشی از ولتاژ نامناسب (چه بیش از حد و چه کمتر از حد) جلوگیری میکند؛ بنابراین، حفظ ولتاژ مناسب نهتنها عملکرد صحیح سیستم را تضمین میکند بلکه از آسیب به تجهیزات نیز جلوگیری مینماید.
برای دستیابی به تنظیم دقیق ولتاژ خروجی، استفاده از سنسورهای ولتاژ جهت مانیتورینگ لحظهای پیشنهاد میشود که امکان اعمال تنظیمات لازم را به مهندسان میدهد. همچنین، بهرهگیری از سیستمهای کنترل دستی و خودکار با الگوریتمهای پیشرفته بهصورت دینامیک، نقش مهمی در بهینهسازی و حفظ پایداری عملکرد سیستمهای صنعتی ایفا میکند.
فرکانس خروجی
فرکانس خروجی به عنوان یکی از پارامترهای اصلی در کنترل سرعت موتور عمل میکند و تنظیم مناسب آن امکان تغییر دینامیک سرعت موتور را فراهم میآورد. این تنظیم دقیق به موتور اجازه میدهد تا در بازههای بهینه کاری عمل کرده و مصرف انرژی کاهش یابد که منجر به بهبود کارایی کل سیستم میشود.
تنظیم فرکانس در عمل با چالشهایی نظیر تغییرات بار و شرایط محیطی روبهرو است؛ به طوری که در هر تغییر، نیاز به تطبیق سریع فرکانس برای حفظ عملکرد موتور احساس میشود. همچنین، هماهنگی بین فرکانسهای مختلف در محیطهای صنعتی پیچیده از اهمیت ویژهای برخوردار است تا تداخل و اختلال در عملکرد سیستمها به حداقل برسد.
شیب راه اندازی و توقف (Ramp-Up/Down)
شیب راهاندازی به دوره زمانی افزایش تدریجی فرکانس یا ولتاژ از حالت سکون تا رسیدن به مقدار نهایی اشاره دارد که تنظیم صحیح آن از اهمیت ویژهای برخوردار است؛ زیرا شیب مناسب موجب کاهش ضربههای مکانیکی و جلوگیری از ضربههای ناگهانی در شروع و توقف موتور میشود که در نتیجه به افزایش عمر و کاهش استرسهای مکانیکی موتور کمک میکند.
برای دستیابی به شیبهای بهینه، تعیین زمانهای کافی برای افزایش یا کاهش تدریجی ولتاژ و فرکانس امری ضروری است. علاوه بر این، بهرهگیری از الگوریتمهای کنترل هوشمند و سیستمهای پیشرفته که به صورت خودکار زمانبندی مناسب را تعیین میکنند، میتواند نقش موثری در بهبود عملکرد سیستمهای صنعتی داشته باشد.
فیلترینگ هارمونیک ها و نویزهای الکترومغناطیسی
هارمونیکها و نویزهای الکترومغناطیسی میتوانند عملکرد سیستمهای صنعتی را مختل کرده و باعث بروز مشکلاتی نظیر اختلال در عملکرد تجهیزات حساس و افزایش دمای سیستمهای الکتریکی شوند؛ به عبارت دیگر، تأثیرات منفی هارمونیکها ممکن است باعث کاهش کارایی سیستمهای کنترل و آسیب به تجهیزات الکترونیکی گردد.
برای کاهش اثرات منفی هارمونیکها، مهندسان میتوانند از راهکارهایی همچون استفاده از فیلترهای فعال و غیرفعال مناسب و تنظیم دقیق پارامترهای فیلترینگ بهره ببرند تا کیفیت خروجی بهبود یافته و نویزهای الکترومغناطیسی به حداقل برسند.
نکات کلیدی و چالشهای تنظیم پارامترهای بهینه اینورتر
تنظیم پارامترهای بهینه در اینورترهای صنعتی با چالشهایی نظیر تغییرات دینامیک بار، محدودیتهای سختافزاری و نرمافزاری و نویزهای الکترومغناطیسی مواجه است. تغییرات پویا در شرایط بار میتواند منجر به نوسانات ناخواسته در پارامترهای سیستم شود و محدودیتهای فنی، امکان تنظیم دقیق را محدود کند؛ همچنین، نویز و هارمونیکهای الکتریکی ممکن است عملکرد سیستم را مختل کنند.
راهکارهای پیشنهادی شامل استفاده از الگوریتمهای تطبیقی جهت هماهنگی خودکار با تغییرات بار، بهروزرسانی سختافزارها و نرمافزارهای کنترل برای افزایش انعطافپذیری، و بهرهگیری از فیلترهای تخصصی و تکنیکهای مدرن کاهش نویز به منظور حفاظت از سیستم میباشد.
سخن پایانی
تنظیم پارامترهای بهینه برای اینورترهای صنعتی، یکی از عوامل کلیدی در بهبود عملکرد و بهرهوری سیستمهای اتوماسیون صنعتی است. این مقاله با ارائه یک راهنمای جامع شامل مبانی نظری، نکات کاربردی، چالشها و راهکارهای عملی، تلاش کرده تا چشماندازی کامل از فرآیند بهینهسازی ارائه دهد. با اجرای مراحل پیشنهادی و رعایت نکات فنی، سازمانها و صنایع میتوانند:
- مصرف انرژی را به شکل قابل ملاحظهای کاهش دهند،
- عمر موتور و تجهیزات را افزایش داده،
- عملکرد کلی سیستمهای کنترلی را بهبود بخشند.
همچنین توجه به روندهای نوین فناوری و استفاده از ابزارهای پیشرفته میتواند نقش مهمی در دستیابی به تنظیمات بهینه داشته باشد. در نهایت، با استفاده از این راهنما و مستندسازی دقیق مراحل انجام شده، امکان تکرار و بهبود فرآیندهای کنترلی در آینده فراهم میشود.